Legendarny Model T sprzedał się w ponad 16,5 mln egzemplarzy. Pomysł na metodę produkcji kultowego auta Henry Ford zaczerpnął z... rzeźni.
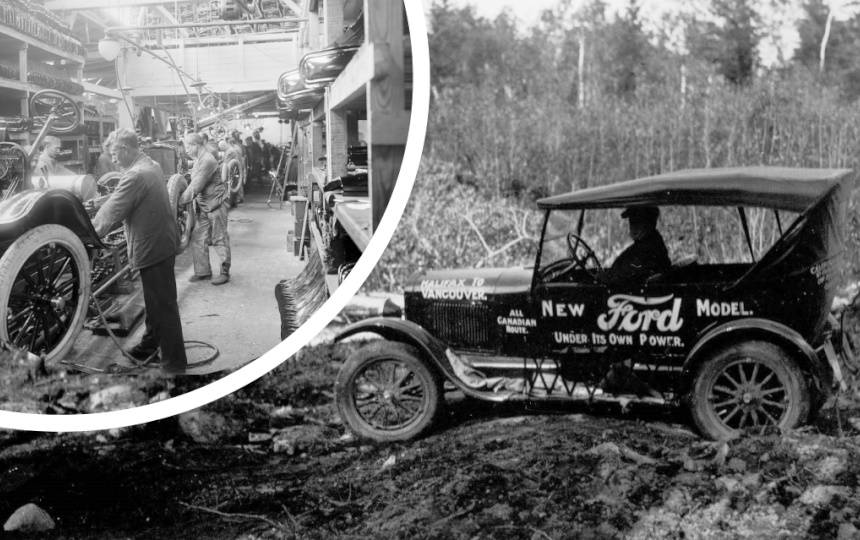
Ostatni egzemplarz „blaszanej Elżuni” („Tin Lizzie”), jak pieszczotliwie nazywano forda Model T, zjechał z linii produkcyjnej w maju 1927 roku. Od chwili powstania pierwszego takiego auta 1 października 1908 roku minęło niemal 19 lat. W tym czasie sprzedało się ich 16,5 miliona. Jak na początek XX wieku był to bardzo imponujący wynik. Skąd brała się popularność tego kultowego samochodu?
Nowa metoda
Sekret Modelu T tkwił w tym, że auto niemalże z roku na rok było coraz… tańsze. W 1908 roku samochód kosztował 850 dolarów. Osiem lat później cena spadła do 345 dolarów, a w 1925 stała się wręcz absurdalnie niska – wynosiła zaledwie 260 dolarów. Jakim cudem? Simon Winchester w książce Siła precyzji. Jak inżynierowie konstruowali współczesny świat pisze:
W przypadku Modelu T Henry Ford postawił sprawy na głowie. Jego celem stało się wyeliminowanie konieczności korzystania z pilników. Chciał, żeby wszystkie części i komponenty trafiały do montażowni perfekcyjnie wykończone, wyprodukowane w zgodzie z wyśrubowanymi standardami tak, że idealnie do siebie pasowały i zbędna była choćby najdrobniejsza korekta.
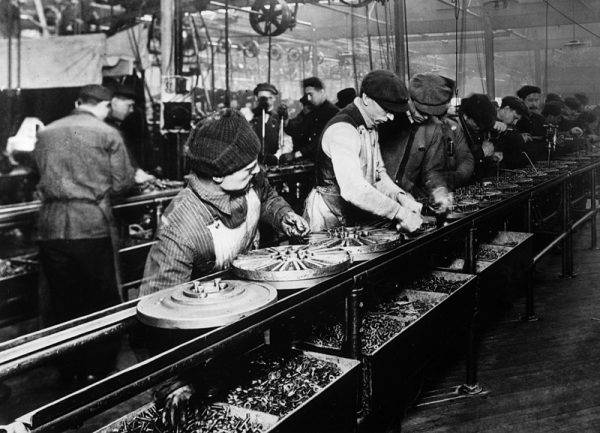
Linia produkcyjna Forda w 1913 roku.
Kiedy już udało mu się zrealizować ten zamysł, opracował całkowicie nową metodę montażu samochodów. Domagał się, żeby części produkowano z precyzją do tej pory rzadko osiąganą, nie wspominając o stosowaniu tak wąskiej tolerancji, a następnie jako jeden z pierwszych powiązał ją z nowym systemem produkcji. Odmienił w ten sposób oblicze przemysłu jako takiego, a z czasem również świata, gdyż zmiana dotknęła wszystkich, wszędzie i na raz na zawsze.
Henry Ford jako pierwszy na świecie wdrożył przemysłową linię produkcyjną na pełną skalę – taką, jaką kojarzymy współcześnie. Było to możliwe dzięki zastosowaniu wysokiej jakości, precyzyjnie wykonanych komponentów, ale nie tylko.
100-elementowa układanka
Nie bez znaczenia był też fakt, że Model T składał się z niespełna stu części, czyli mniej więcej tylu, ile mają dzisiejsze pralki. Dla porównania: obecne samochody są zbudowane z przeszło 30 tys. elementów. Henry Ford przez dwie dekady pracował nad tym, by móc łączyć te „puzzle” w pełni działający automobili w jak najkrótszym czasie – i jak najbardziej efektywnie.

„Wreszcie w 1913 roku nastąpiło objawienie: komponent można przecież położyć na taśmie, a pracownikowi powierzyć jedno proste, niewymagające zadanie, które będzie wciąż i wciąż powtarzane na wszystkich częściach dostarczonych mu za pośrednictwem pasa transmisyjnego” – pisze Simon Winchester. Ponoć pomysł na taką organizację pracy genialny konstruktor aut zaczerpnął z… miejscowej rzeźni, gdzie właśnie w taki sposób oprawiano wieprzowe tusze.
Czytaj też: Najbezpieczniejszy zamek świata? Przez niemal 60 lat nikt nie był w stanie go otworzyć!
Oszczędność czasu
Na początek wprowadzono to rozwiązanie przy montażu iskrownika do Modelu T. Było to proste urządzenie zbudowane z magnesu i dwóch cewek zapłonowych. Ford kazał postawić przy stanowisku montażowym przenośnik taśmowy, wzdłuż którego poszczególni robotnicy, odpowiedzialni za jedną, konkretną część, instalowali poszczególne elementy. W książce Siła precyzji czytamy:
Dotychczas pracownik potrzebował dwudziestu minut, żeby złożyć cały iskrownik. Po wprowadzeniu linii produkcyjnej obsadzonej robotnikami wykonującymi indywidualne, otępiające zadania, ten czas zredukowano do pięciu minut. W dodatku wszystkie iskrowniki wychodziły dokładnie takie same. Nie miało znaczenia, w jakim nastroju jest pracownik ani czy myślami jest już w domu – komponenty idealnie łączyły się z silnikiem Forda i nie było nawet cienia wątpliwości, że coś się wysunie bądź odłączy.
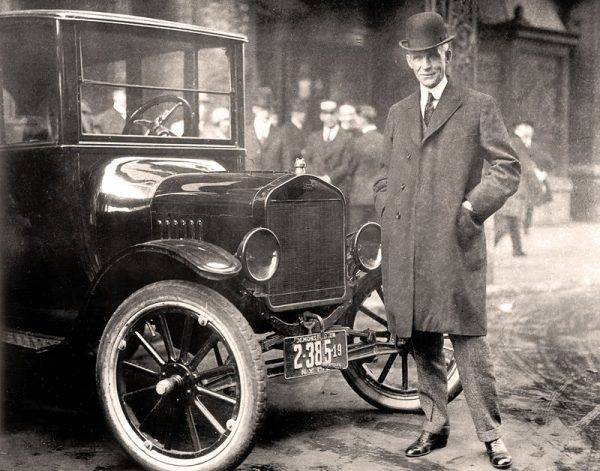
Henry Ford ze swoim flagowym samochodem w 1921 roku.
W 1915 roku tę metodę montażu wprowadzono również przy składaniu osi, co pozwoliło na skrócenie czasu potrzebnego do złożenia komponentu z dwóch i pół godziny do zaledwie 26 minut. W przypadku skrzyni biegów zastosowanie linii produkcyjnej obniżyło czas o równo połowę, a zbudowanie przemodelowanego silnika zajmowało robotnikom przy taśmie cztery godziny – zamiast wcześniejszych 10! „Przyszedł taki moment, że przez bramę fabryki zlokalizowanej w Dearborn co czterdzieści sekund wyjeżdżał nowy Ford Model T” – komentuje Simon Winchester.
Czytaj też: „Meble, mały fiat – oto marzeń szczyt”. O popularnym maluchu, który stał się naszą codziennością
Cięcie kosztów pracowniczych
Henry’emu Fordowi przy okazji tej oszczędności czasu udało się zaoszczędzić również na czymś innym, nie zmieniając materiałów produkcyjnych ani konstrukcji swojego flagowego samochodu. Otóż niemal całkowicie wyeliminował koszty… szkolenia robotników. Praca przy linii montażowej nie wymagała wszak w zasadzie żadnych szczególnych kwalifikacji. Ja konkluduje Simon Winchester w swojej książce:
Henry Ford za jednym zamachem rozwiązał kilka problemów. Dzięki linii produkcyjnej mógł zbudować znacznie więcej samochodów, zredukować koszty jednostkowe, stopniowo obniżać cenę wozu, aby więcej osób mogło sobie pozwolić na zakup auta, a tym samym zyskać popularność i zdominować rynek.
Źródło:
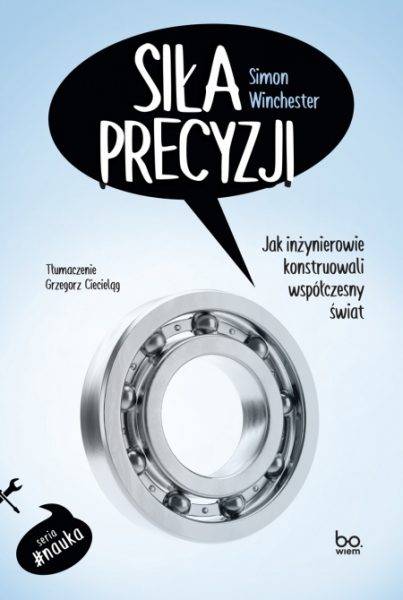

Źródło ilustracji otwierającej tekst: Peter Elfelt/domena publiczna; Edward William Flickinger/domena publiczna
KOMENTARZE
W tym momencie nie ma komentrzy.